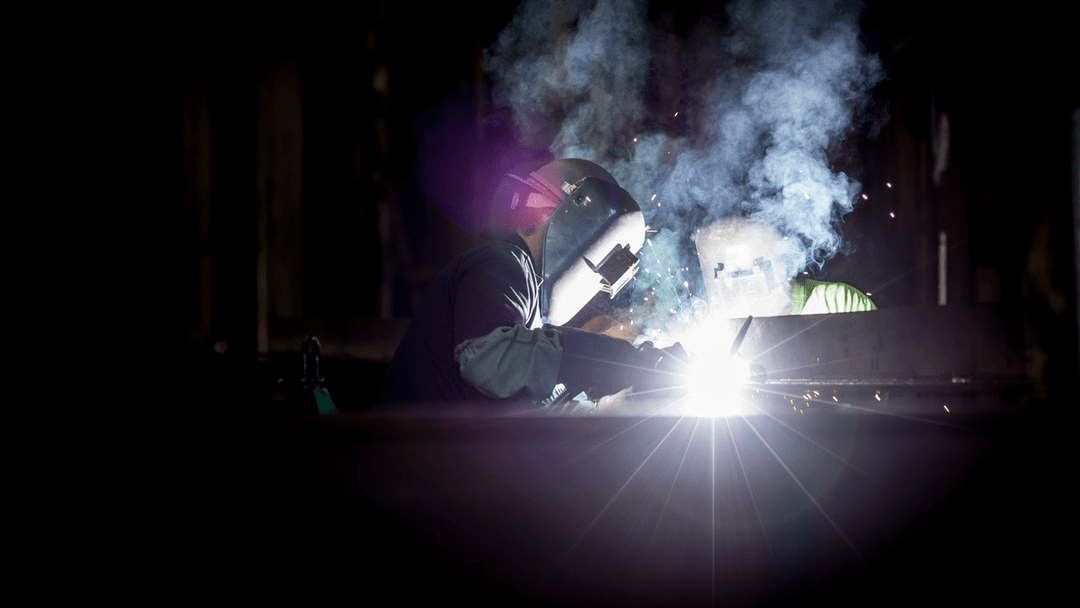
The growth and usage of plastics have continued to gain popularity around the world in various manufacturing operations. They are very suitable for creating different products and also meeting the design requirements during the manufacturing processes. However, for the plastics to meet the intended purposes, they have to be melted and joined through laser welding processes. It is in this case that the laser welding thermoplastics come in place. Laser welding of thermoplastics is generally meant for joining molded thermoplastics to form the final products that will be used to create various items to be used in different applications like creation of containers, packages, cups, boxes, and many others. There are two major forms of this type of welding for thermoplastics that every reader needs to know about. These are known as the direct laser welding of thermoplastics and the transmission laser welding options. Both come with different properties to ensure that the final results are achieved. The skills and expertise of the designer or engineer also matters a lot when it comes to this form of a laser welding. This, therefore, implies that the designer must have a vast understanding of this type of a technology in order to achieve the desired results.
There is a range of benefits and advantages that come with this solution. This article also intends to enlighten readers more about the advantages and applications of the laser welding of the thermoplastics. The first reason why it is very important is that it helps in promoting efficiency in the creation of the packaging materials like boxes, containers and other final products. Note that as said above, the main reason why this form of a wedding is very essential is that it helps in joining molded plastics. It becomes very easy and fast for the manufacturer to use the molded thermoplastics in creating the above-mentioned materials and meet the individual needs, requirements and expectations of the final customers. The introduction of this form of welding has also minimized the wastes of plastics in the manufacturing processes. Most of the molded thermoplastics are fully utilized in the manufacturing processes, resulting in maximum saving and less wastage in the long run. It has also become very easy for the manufacturers to customize different designs of the products or items made from the plastics, and this has been easily achieved as a result of the introduction of the thermoplastic welding options.
The fact that the customization of the items manufactured has made it easier for many manufacturers to meet the individual needs and expectations of their customers. It is obvious that many people buying containers, cups, plastic tanks, and others will be attracted to a range of different designs of these items. This type of laser welding thermoplastics has also eliminated so many miscellaneous costs and cumbersome part features in many plastics, thus making it easier to manufacture the final products. The elimination of unwanted and tedious part features also results in an improvement of the final aesthetics or curb appeal of the manufactured products. Quality assurance also comes with this form of laser welding.